Warwick University Campus
OCTOBER 15TH 2019
The aim of the evening was to consider how the UK automotive industry can establish an indigenous supply chain for electric vehicles, keeping in mind the consequences if it fails.
Seventy guests attended. After-dinner conversations continued for a long time before some re-grouped at the nearby hotel bar for night caps.
WMG Warwick Manufacturing Group
WMG’s position as an automotive centre of excellence means Warwick hosts many conferences, which is reflected in the professionalism of the Conference staff. The venue itself is very functional, which is not typical of our usual more whimsical choices, but it was suitable for such an industrially-focused dinner, at the heart of the automotive innovation cluster, anchored on the Warwick Manufacturing Group and the Advanced Propulsion Centre.
SPEAKERS
PROFESSOR DAVID GREENWOOD: Head of the Advanced Propulsion Team at WMG and of APC’s Electrical Energy Storage Spoke.
RICHARD HANKINSON: Automotive Director at Unipart Logistics.
ISOBEL SHELDON: Head of Business Development at the UK Battery Industrialisation Centre (UKBIC).
DR GERO KEMPF: Chief Engineer at JLR and Industrial Professor at WMG.
Foreword to the Dinner
What did we hope to achieve at the dinner? Mainly it was to clarify whether a full supply chain was possible which could support a domestic EV manufacturing industry. Thanks to the speakers and discussion which followed, a clearer picture did present itself, which was largely positive, but the next 2-3 years will tell whether this is true or wishful thinking.
All about the battery
The battery is the essential component in the whole supply chain picture, as Professor Dave Greenwood explained, calling it the “defining component”, because it accounts for 40% or more of the build cost. Unless there is a battery supply chain in the UK therefore, there will not be an EV industry to replace the current automotive industry, putting at risk the future of about 190,000 manufacturing-related jobs.
JLR’s Good News
The key to it all, in my view, lies with JLR. Imagine if JLR had “done a Dyson” and planned to establish all of its EV assets in Eastern Europe, leaving only a central R&D function and marketing in the UK. It is a temptation for JLR because the heart of the automotive industry and its supply chains are located in Germany and the East European hinterlands where they are already building Giga battery factories. It was indeed partly due to the lack of a supply chain that JLR contracted Magna Steyr to manufacture its first EV, the I-Pace, in Austria. However, the good news is that, despite the temptation, JLR has clearly stated that it will make the UK the centre of its EV future plans.
Government support
The government’s clear resolve to support the transition of the automotive industry to an EV future must surely have played a critical part in the decision by JLR to remain a central part of this future. It is noteworthy that one of the first things Boris Johnson announced on becoming Prime Minister was the government’s commitment to the EV industry, which has been followed by a new extra package of funding for the Faraday Battery Challenge of £1bn.
Faraday Challenge
Within the government’s Faraday Challenge the centre piece is the funding for a Battery Industrialisation Centre (UKBIC), a key purpose of which is to create the conditions to encourage battery manufacturing in the UK by both domestic and inward investors. The Centre is doing this by helping to develop new supply chains and by providing training support for a future battery workforce.
Singapore here?
Isobel Sheldon of UKBIC pointed out in her talk that there are enough potential suppliers of battery materials and components in the UK to make a domestic supply chain feasible. If these supply linkages can be enabled and strengthened, it will help attract a Giga factory to invest in the UK, by giving them access to a second source of suppliers and alternative battery solutions. This was a major reason Dyson originally chose Singapore over the UK to establish its EV manufacturing centre, even though Singapore is a high cost location. If the UK supply chain is strong enough therefore it can attract the scale of investment and even become an export base for Europe as well. The example of Singapore can serve as a pointer in this respect.
Battery materials
The UK is a world leader in battery materials. The Faraday Challenge’s Faraday Institute supports around 20 of the leading battery teams at universities across the UK; Johnson Matthey is a global leader in cathode battery materials; and Dyson is a major innovator (but for its internal programmes). There are also several world class startups and spinouts, several of whom attended the dinner.
E-Drives
The next most important component is the Electric Drive Unit. Like batteries, these also require supporting technologies to squeeze out optimal performance, notably high performance power electronics, processors, and related software. Here the UK is particularly strong leveraging the skills from motor sports, Formula-1 and Formula-E. This adds in turn to the attraction for inward investors to engage with the UK supply chain.
Collaboration
Scale, however, is required to turn these technical strengths into opportunities that benefit the whole of the automotive/EV industry. Acquisitions generally don’t achieve this. Much better is collaboration. For example, the tie up between BMW and JLR to share expertise and a supply chain for electric drive train technologies could easily be extended to batteries. Tata has made clear it will use collaborations to ensure that JLR can keep its ambitious Destination Zero programme on track.
Sovereignty
I would argue finally that for a ‘Sovereign’ supply chain to develop it is vital that JLR remains independent (under Tata) because in this way there will be a large enough company at the centre of the UK automotive industry to provide leadership and direction to the wider supply chain – even though this will of course be a global supply chain – but it will still be anchored in the UK, with serious manufacturing, not just R&D. For these reasons it was greatly appreciated that Dr Gero Kempf of JLR joined us during the evening to share his thoughts and to encourage us.
SELF-INTRO SESSION
Alex introduces the Self-Intros which are an opportunity for selected members and special guests to introduce and update us on their activity; the effect is to build a sense of anticipation about the evening and to help people identify who to meet.
SELF-INTRODUCTIONS
Adam Huckstep, Founder and CEO of Hypermotive Ltd, Loughborough
Iain Mosely, Head of Technology, Charge Point UK, Reading
Ryan Maughan, CEO of AVID Technology Ltd, Newcastle
Philip Johnston, Founder and CEO of Trackwise Plc, Tewksbury, Gloucs
Paul Faithfull, Founder and MD of Potenza Technology Ltd, Coventry
Giles Salt, CEO of M&I Materials Plc, Manchester
Vic Kist, CEO of Saietta Ltd, Oxfordshire
Christoph Birkl, Co-founder and CEO of Brill Power Ltd, Oxford
Ian Constance, CEO of the Advanced Propulsion Centre (APC), Coventry
SELF-INTRO SNAPS
- Ian Mosely, Charge Point
- Adam Huckstep, Hypermotive
- Philip Johnston, Trackwise
- Vick Kist, Saietta
- Ryan Maughan, AVID Technology
- Paul Faithfull, Potenza Technology
- Ian Constance APC
- Giles Salt, M&I Materials
- Christoph Birkl, Brill Energy
NETWORKING SNAPS
- Chris Wright, Faradion Ltd (left) Nick Rodgers, Productiv (centre) Nicky Godding, Business & Innovation Magazine (right)
- Philip Johnston, Trackwise Ltd (left) Adam Huckstep, Hypermotive Ltd (centre) Terry Spall, Horiba-MIRA
- Mark Turner, M-Solv Ltd (left) Scott Roberts, Polar Technology Group (centre) Janet Donovan, M-Solv Ltd (right)
- Charles Johnstone, Hexadex Ltd (left) Pete James, Lyra Electronics Ltd (centre) Giles Salt, M&I Materials Ltd (right)
- Iain Mosely, Charge Point (left) and Sam Cockerill, Libertine FPE Ltd
- David Alcraft, Alcraft Motor Company Ltd (left) and James McGeachie, ProDrive Ltd
- Clive Warren, Renishaw plc (left) and Ryan Maughan, Avid Technologies Ltd
- Nick Russel, Denchi Power Group (left) and Adam Holland, JCB Power Products
- Chris Wright, Faradion Ltd (left) Nick Rodgers, Productiv (centre) Nicky Godding, Business & Innovation Magazine (right)
Isobel Sheldon – UK BIC
Isobel was founder and director of a battery startup, Amberjac Projects Ltd, from 2002 to 2013, which among other things worked on developing the world’s first commercially available PHEV based on the Toyota Prius. It was carrying out battery development work for a number of OEM’s when the global financial crisis resulted in revenue drying up and business closure. Isobel then joined Ricardo as a battery specialist on the business development side. Two and a half years later she moved to the role of Engineering and Technology Director at Johnson Matthey’s Battery Systems. After JM sold the business to Cummins Inc, she became Director Technical Market Development at the Cummins unit, until the chance arose to head up Business Development at The UK Battery Industrialisation Centre (UKBIC). Isobel is therefore one of a handful of people in the UK with a long and deep battery background, several of whom are at UKBIC, now helping to build the UK’s battery industrial capability.
The battery cell (made up of the anode and cathode separated by a separator and containing electrolyte) form the battery core. In the UK, AGM Batteries Ltd, in Scotland, has the means to make cells from powder to finished cells, while the AESC plant in Sunderland, now owned by Chinese group, Envision, imports the cell electrodes from Japan to assemble in to cells, modules and packs. Shipping very high volumes of sensitive material (lithium) over long distance is problematic, however: the carbon cost of transport is high; and there is the risk of degradation. This means production in the UK or Europe is the best option moving forwards.
The aim of UKBIC is to create the conditions to enable battery production in the UK via: 1) an Open Access facility where companies can trial and manufacture new batteries from powders through to cells and packs; 2) to encourage a domestic supply chain; 3) to train up the future workforce for Gigabattery factories.
The Centre will have around 1GWh of capacity (the Nissan factory has around 1.7GWh). Isobel expects as much as 70GWh to 120GWh will be needed by the mid-2020s, just in the UK alone. It can cost up to £1.5bn to establish a Giga factory and payback may take as long as 10 years, which will make it challenging for revolutionary battery technologies to gain adoption over that period. As a result, lithium-ion is expected to dominate for at least 10 years, supported by production scale and falling costs.
UKBIC is working with the Advanced Propulsion Centre on building up the UK battery supply chain, which includes existing assets, such as: a nickel refining plant in South Wales; a major supplier of needle coke (for synthetic graphite) in Lincolnshire; anode/cathode foil making; and the chemicals industry, which could supply battery materials to UK and European plants. This creates conditions as well to attract inward investment by a Gigabattery factory.
Richard Hankinson – Unipart Logistics
Richard opened by saying this is the most exciting time he has ever known in his automotive career, most of which has been spent at Unipart, where he is currently Automotive Director at Unipart Logistics. Unipart divested from British Leyland in the mid-1980s in a management buyout and remains a private company, majority owned by its employees. John Neill, who led the buyout, and is still Chairman and Group CEO, was from the first deeply influenced by the way of working of the Japanese car industry which is what led him to instituting the Unipart Way. It also helps explain why Unipart continues to do things differently.
Unipart for example have recognised that the End of Life management of batteries is an elephant in the room. As Richard explained, if all of the 31 million cars on UK roads were battery powered it would require 208,000 tons of cobalt, double current global production, and 2.4 million tons of copper. Globally, by 2040 there are estimated to be 56 million EV cars sold, 500 million of them on the road. How therefore to reconcile this without drastic action and innovation? One solution is to replace cobalt, which is where Johnson Matthey has leading technology; another is to recycle the lithium, cobalt and other strategic materials until a new generation of battery materials can replace lithium-ion.
This presents three options for Unipart:
1) Battery repair: which would probably have to be carried out by specialist service companies. Unipart is responsible for all the aftermarket logistics for the Jaguar I-Pace for example and handling damaged batteries is a complex and costly issue today.
2) Re-Use: it is possible to use EV batteries for home energy storage linked to solar power generation. As the government has now removed the fiscal incentives of selling surplus power to the grid this has become more attractive.
3) Recycle: this is still a huge challenge, as the industry does not yet have the solutions to recycle all of the battery components economically or at scale. Unipart is discussing collaborations with several companies to deliver a solution to this.
Richard wanted to make clear the End of Life challenge was a “huge opportunity for the UK”, and would assist the development of a full domestic EV supply chain. What no-one wants to see, he added, is exporting used batteries to Europe only to import the raw material component parts back again.
Prof Dave Greenwood – WMG
Prof Greenwood has a reputation as the most knowledgeable person about the EV industry in the UK. We were fortunate therefore to have him speak to us given the calls on his time, which includes running the Advanced Propulsion programme at WMG, and meeting with the many important customers of the Centre, such as JLR. Holding the dinner on the Warwick Campus underlined the strong association of the dinner with WMG.
Dave began by putting into perspective the pace of change that has occurred in electric vehicles. For example, six years ago it was still whether not when would there be electric vehicles on the road. Now the answer is obvious, and the government is helping to lead the charge, having signed a legal mandate to go to zero net carbon emissions by 2050. What this means is no internal combustion engines beyond about 2040, which “represents a tremendous pace of change”. What started as regulatory push is now consumer pull as people start to use EVs as an “everyday vehicle” at a cost which is becoming affordable for most people.
The three major components to design and manufacture an electric vehicle are: an electric motor, the power electronic system, and the battery. Of these, the battery is “the defining component” around which the car is designed. It weighs over half a ton; it determines the range, cost, performance and the lifetime of the car; it accounts for 40% or more of the build and materials cost of the car; this is about 3-5 times the cost of a car engine, which most OEMs consider to be critical to brand value, as well as critical to produce themselves.
The UK makes almost 2 million cars a year. In about a decade’s time, that could equate to about £5 billion pounds a year, just to supply the cars built in the UK, and ten times that across Europe. This is a new market displacing and building on the older market of petrol engine cars, which provides opportunities for small and innovative companies to bring technologies forward and find new pathways to market.
Car production volumes are currently still relatively low, at around 10,000 cars a year, so it is possible to ship batteries all over the world – often from Asia – but as production scales to 100,000, or half a million cars, it doesn’t make sense to ship hazardous goods that weigh half a ton to half a million vehicles around the world. Instead it makes more sense to make them nearby, ideally in the same country where manufacturing is located. Therefore, if the UK is successful in creating a battery manufacturing industry it has a big market to go for locally, and potentially into Europe. But if unsuccessful there is a risk that car assembly may move to the plant closer to the battery manufacturer. If that’s in Europe, the UK could find itself left “building out a legacy of internal combustion engines.” In other words, as he reminded us, “there is everything to play for and everything to lose.” This is why Boris Johnson in one of his first speeches as PM, talked about the strategic opportunities for batteries; and why very recently the government announced a further investment of one billion pounds to secure the supply chain further.
Why should the UK have a chance to do all this, he asked? He pointed to the experience around the Nissan Sunderland plant, which used to be Europe’s largest battery assembly plant; the quality of research at UK universities and start-ups; how JLR has committed to produce Electric Drive Units at Wolverhampton and to assemble battery packs at Coleshill. “There is a commitment in the UK, so we need to build the industry behind this to make it happen”, he concluded
This is the opportunity therefore for the supply chain. The chemical industry for example could re-engineer what they already make, like paints and adhesives, into battery materials. There needs to be a Gigafactory which processes the materials into cells. “This is why it is important to land one of those gigafactories in the UK in the next five years as this is the timeframe when big manufacturers will place their bets.” He added that the UK government is reserving a significant amount of money to try and make that happen.
Battery cells then need to be integrated into module packs. This is an area where the UK has a lot of expertise serving the high value, low volume market of motor sports. He gave examples of some of the companies in the room, like Delta Motorsport, Williams, Trackwise, Potenza, and so on. The market is still small today which is why it is important to be in at the beginning, while the costs of entry are low, in order to follow the growth curve without having to make massive investments to take on massive competitors ten years down the line.
Battery materials at their end of life is also part of the supply chain. It is neither sustainable nor economic to be continually digging up minerals. Similarly it doesn’t make good sense to send old batteries over the Channel for recycling to bring back again to manufacture batteries.
To illustrate the speed at which battery technology has advanced, in 2010 a battery would have cost $1000 per KWh, and it is now $200 or less at pack level. There is still space for a two fold reduction in cost, he added, which is now likely to come from technology rather than pure volume. Batteries also have twice as much density as 10 years ago, which means twice the range compared to 2010. Projecting forwards therefore it is possible to see EVs going from 4-5% of the market to 50% or even 70% of the market in the longer term future.
Lithium-Ion batteries are likely to be the dominant chemistry for the next 8-10 years “at least”, because it takes about that time to transfer a new chemistry from lab to final product. The two batteries to watch are Sodium Ion and Solid State batteries. Once these can be “demonstrated properly” it will take about 3-5 years to bring to market.
The EV industry is the focus of battery manufacturers because it is such a high volume market. Other sectors, however, are becoming important. Aerospace has come from “doing almost nothing in electrification 12 months ago to where it takes about 40% of my test capacity in laboratories on the WMG site”. There is also the emergence of rail, off-highway and bus.
The market he is really watching for volume, however, is the stationary energy storage market, he said. This is being held back by the way the grid is currently regulated, but it is becoming likely that the regulations will change and then multi-billion dollar industries will move into the field. It will then open a major new frontier in terms of the types of technologies needed.
To sum up, he thought the UK has “a pretty good chance to grab a big slice of the battery and supply chain industry” and added that he hoped the dinner would show how many more companies could be a part of that opportunity.
Dr Gero Kempf – Jaguar Land Rover
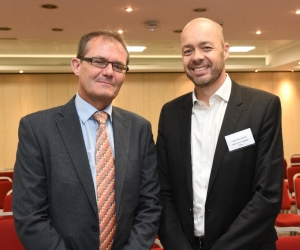
Dr Gero Kempf on the left, next to Ian Constance, CEO of the Advanced Propulsion Centre (APC)
Gero kindly agreed to participate at the dinner in the capacity of ‘commentator’ to share his views from an OEM and personal perspective. I am grateful to Ian Constance at the Advanced Propulsion Centre for making the introduction to us.
Gero is an independent-minded thinker who I had the opportunity to hear speak at an EV event in London earlier in the year. As Chief Engineer of Jaguar Land Rover he has the ear of the CEO, Sir Ralf Speth. In fact, it transpired during his talk that an important reason for this is that he dares to be different.
Gero joined JLR in 2015 after a career spent at BMW’s HQ in Munich. He was invited to become a professor at WMG at the same time as Ralf Speth, in September 2016. The appointments underline the special relationship which exists between WMG and JLR, forged since the Tata Group acquired ownership of JLR in 2008.
A particular focus of Gero’s comments was on the value of looking around for the best information, and not trying to take all the credit for oneself. He gave the example of how he was able to make use of information at a meeting of a think tank he attended in Germany, which served him later extremely well at JLR. His point was it is okay to borrow ideas from people who have better ones. “Be humble”.
A strength of Germany, he noted, is its focus on fundamental science, so this provides opportunities for collaboration. Other opportunities to transfer knowledge come along, such as after Diesel Gate, when Bosch closed some of its related activities and JLR was able to benefit by recruiting valuable staff. Similarly, Japanese expertise in battery manufacture has been transferred to the Sunderland plant. Both are examples of how information is shared and circulated.
He was keen to emphasise that Europe has everything to build a strong supply chain, including its own materials; therefore it doesn’t need to follow China. Using outside of the box thinking it is also possible to do things better and differently. He gave an example of how to improve battery performance, and added, “This is why Ralf likes me”.
Supply chains need to be localised – and quickly. To do this collaboration will be the watchword. On this point Gero was privately encouraging about what the Bessemer Society is doing, which he called “bringing together new thinking, challengers, and entrepreneurs, to share and learn together”.
DISCUSSION PERIOD
From Gero’s commentary we transitioned to open floor discussion. Views expressed included:
There is a greater get up and go energy around than 10 years ago – but the problem of investment in manufacturing and capital goods remains. For example, not so long ago the UK had four aluminium manufacturing facilities, now there are none, despite aluminium being a core part of the automotive supply chain. The problem is capital is unwilling to invest to bring any of them onstream again. Another complained about the decision by Tata Steel to close a plant in South Wales which made special steel for transformers, due to unwillingness to invest [although I heard separately that it was more a case of the Tata group re-allocating resources internally].
Horiba-Mira told us that over the last 2-3 years they have secured approximately 140 acres of additional land, large enough to support a Gigafactory scaled to UK needs as well as an EV manufacturing plant. The problem is the UK faces competition for Asian investment from East Europe. It should be made a priority therefore to organise an industry-government task force to promote globally what the UK can offer. Delays to Brexit however are not helping.
The extra demand for electricity for vehicle charging is at risk of holding back the progress of the EV industry. One of the companies that develops fast charging technologies pointed out how a smart charging network can optimise the management of demand for power. Another how new service paradigms, such as car sharing and autonomous vehicles, would solve some of the charging and infrastructure issues.
On May 22nd apparently the number of electric charging points in the UK outnumbered the number of petrol pumps in forecourts. This kind of information could be used to reduce the problem of range anxiety, and therefore should be made more widely known.
An SME in the supply chain said they found it harder working with OEMs in the UK than in Europe and the USA – although adding they were now starting to make progress with JLR. An advantage of the American market is scale. A niche market like ice machines for Ice Rinks for example is big enough to create sufficient demand. On the other hand, a niche market in the UK like buses has shrunk to the point where it has become a sub-critical size.
Thinking differently is the strength of innovation-led startups. One company pointed out how they approached lightweighting from a different angle; another about rapid charging using a combination of lithium-ion and supercapacitors. One company explained how they were designing a new kind of battery to reduce weight, but that to transition from the small scale development stage to mainstream they had to go to Asia – at least until the infrastructure promised by UKBIC is fully operational. Recruiting the right process engineers is also what takes them to Asia. The Swedish startup, Northvolt, which is building a Gigafactory in Sweden, has addressed this by working with VW and BMW and hiring senior execs from Sony, Samsung and other Asian cell majors.
ACKNOWLEDGEMENTS
Sincere thanks to our Sponsors who made the dinner possible.
LEAD SPONSOR
DINNER SPONSORS
Forresters is a leading IP law firm, founded in 1884 in Birmingham. It now has offices as well in London, Liverpool, Southampton and Munich.
Consilium Recruit is a recognised authority in the recruitment of engineering, management and industry executives for the Automotive, Aerospace, Manufacturing and Innovation sectors.
Our four supporters represent important contributors to the eco system infrastructure: The Advanced Propulsion Centre is mobilising innovation through funding of research partnerships involving SMEs and OEMs; Unipart Logistics is a key part of the automotive supply chain; Productiv Ltd provides manufacturing scale up facilities for innovation companies; iPro Solutions supports innovation companies with contract manufacturing and logistic services.
Alex Stewart
October 30th, 2019